www.engineering-russia.com
21
'18
Written on Modified on
Контроль текущего состояния подшипников улучшает процесс шлифования
Контроль текущего состояния подшипников позволяет не только определить потребность в их замене, но и сделать выводы о состоянии всего станка или системы. Чтобы продемонстрировать преимущества сервиса контроля текущего состояния (CMS) от компании NSK, пользователям шлифовальных станков предлагается два случая его практического применения.
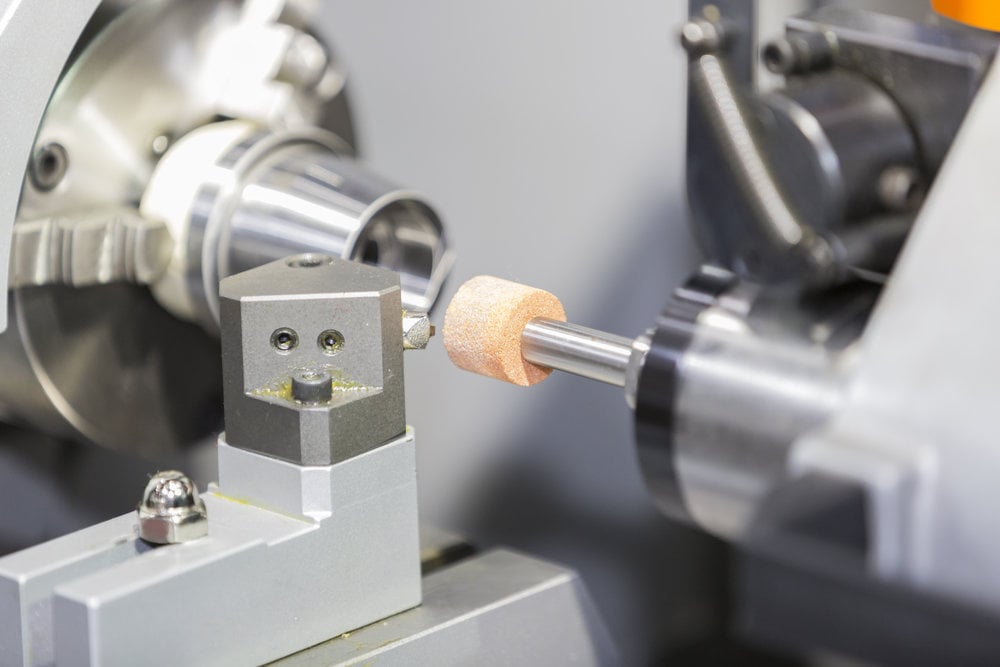
В рамках программы NSK по улучшению основных средств (AIP+) CMS является методом определения состояния компонентов машины, таких как подшипники, без прекращения эксплуатации оборудования. Специально разработанная для этой цели измерительная система фиксирует уровень вибрации, температуру и частоту вращения компонентов машины и анализирует их с помощью современного программного обеспечения, которое создает базовые данные для оценки расчетного срока службы подшипников и отображает информацию, например, о недостаточном количестве смазки, наличии вмятин или ошибок выверки. Эти данные служат более точной характеристикой состояния всей системы или процесса.
Данные о процессе также можно использовать для определения (или хотя бы локализации) причин дефектов формы, возникающих при шлифовании. NSK применила этот метод на собственном заводе в Великобритании. В этом случае дефекты формы наблюдались на станке, выполнявшем шлифование дорожек качения подшипников. После нескольких попыток ремонта и безуспешного поиска неисправностей специалисты предположили наличие дефектов подшипников. В поисках окончательного ответа NSK решила провести анализ текущего состояния с помощью CMS.
После считывания данных привода и учета значимых факторов, таких как характеристики подшипников и двигателя, были выполнены измерения до и после замены подшипников. Анализ показал, что ни шпиндель, ни шпиндельная головка устройства правки не были причиной дефектов формы. Это избавило технический персонал от необходимости многочасового полного демонтажа шпинделя. Вместо этого специалисты быстро обнаружили настоящую причину проблем, после чего никакие дефекты формы дорожек качения или качества обработки поверхности больше не появлялись.
Суммарно удалось сэкономить три рабочих дня, которые потребовались бы для полного демонтажа шпинделя и обследования подшипников, не говоря уже о сопутствующих потерях рабочего времени на каждом связанном производственном участке. В результате экономия затрат на проведение технического обслуживания и потерь от простоя составила 13 080 евро.
Во втором случае пользователь бесцентрово-шлифовального станка заметил появление ошибок при работе. Специалисты по обслуживанию данного станка заподозрили наличие дефектов в некоторых подшипниках шпиндельного узла. Так как в шлифовальном шпинделе применяются различные подшипники восьми типоразмеров, было решено использовать метод CMS от NSK, чтобы помочь специалистам обнаружить неисправные подшипники и найти окончательное решение проблемы.
Анализ, выполненный после измерения основных параметров технического обслуживания во время работы станка, показал, что подшипники шпинделя не были причиной дефектов формы. После этого специалисты по обслуживанию занялись обследованием других компонентов, и пользователь сэкономил два рабочих дня, которые потребовались бы для полного демонтажа шпинделя, а также избежал сопутствующего простоя. Общая экономия составила 33 600 евро.
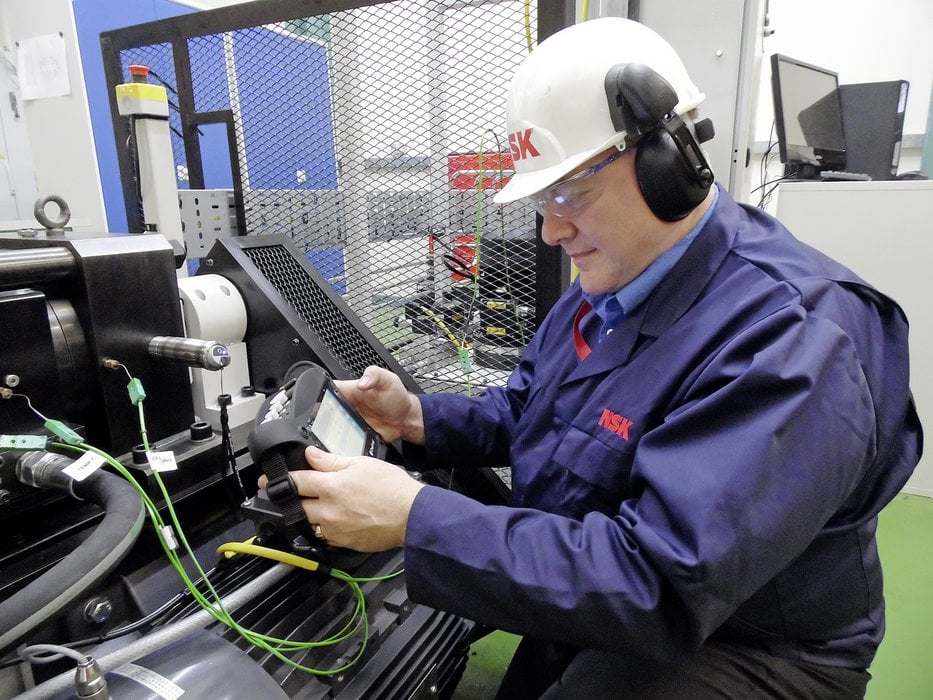
S042018-N-Image2.jpeg - Сервис контроля текущего состояния от NSK помогает определять причины нарушений при шлифовании
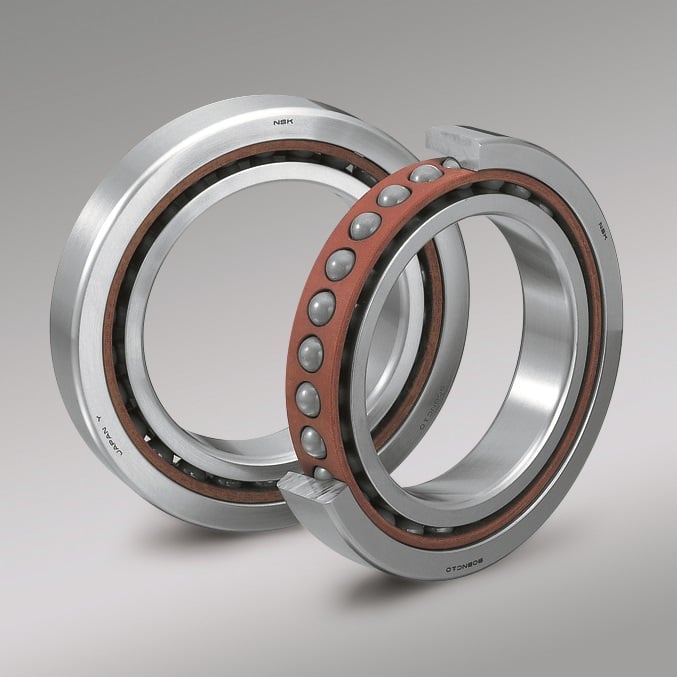
S042018-N-Image3.jpeg - ACBB от NSK - сверхвысокоскоростные радиально-упорные шарикоподшипники серии ROBUST
Получите дополнительную информацию…